RFID inventory management is changing the way businesses keep track of stock by providing real-time visibility, automation, and greater accuracy. Using RFID allows companies to scan multiple items simultaneously, streamline daily operations, and reduce errors, making inventory management faster and more efficient.
In addition to improving workflow, RFID inventory management solutions allow businesses to gain insights into customer purchasing trends, minimize labeling mistakes, prevent loss, and simplify the ordering process.
As more industries integrate RFID technology, it’s becoming a key tool for better supply chain management and inventory control across various sectors.
What is RFID Inventory Management?
RFID stands for Radio Frequency Identification. It is a technology that uses radio waves to read and capture information stored on a tag attached to an object. These tags can be read from a distance, which means that unlike barcodes, they don’t require direct line-of-sight to be scanned. For inventory management, RFID offers an automated and efficient way to keep track of stock levels, product locations, and the movement of goods.
How Does RFID Inventory Management Work in a Warehouse?
In a warehouse setting, RFID technology enables automated inventory tracking using RFID tags, readers, and a central database. Here’s how it works:
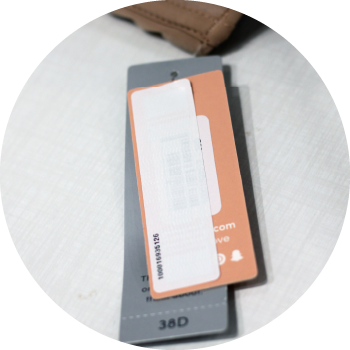
1. Tag Items
Each product, pallet, or case is tagged with an RFID chip that stores a unique item code.
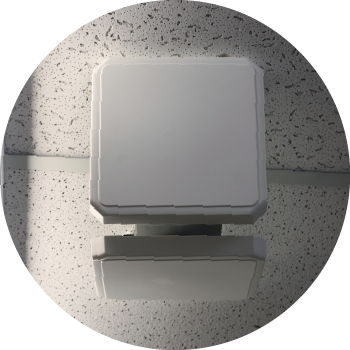
2. RFID Readers
Fixed or handheld RFID scanners detect tags automatically without requiring manual scanning.
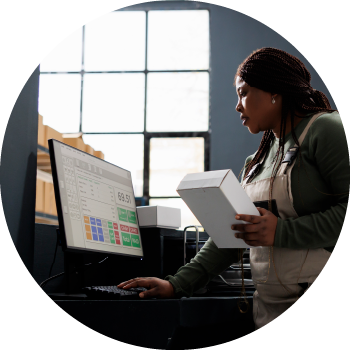
3. Data Collection & Processing
The scanned data is transmitted to inventory management software, allowing real-time updates and tracking.
Features of RFID Inventory Management
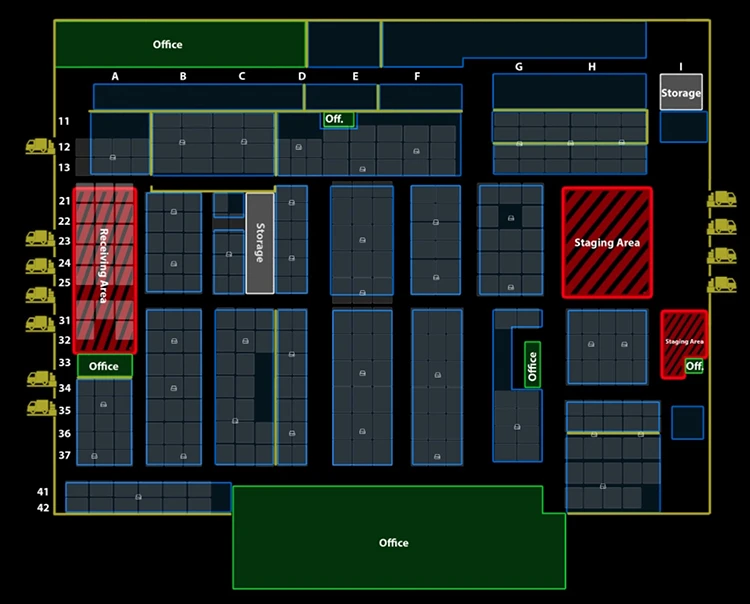
Real-Time Visibility: Modern RFID technology like Portal Track offers instantaneous data delivery through passive and active RFID devices. This data can then be displayed on custom software dashboards and map displays on different kinds of devices, giving you a consistently up-to-date, accurate picture of your inventory.
Event Monitoring: Event monitoring refers to the generation of real-time actions and notifications that help to safeguard operations procedures. These notifications include video and email-based notifications and alerts that are triggered when different types of conditions present themselves based on real-time data. For example, you can receive alerts when an item reaches stock below a certain number.
Pinpoint Accuracy: When it comes to accuracy, nothing is better than the latest RFID technology. Modern systems can track and locate inventory items and other assets so that operators can pinpoint the location of items within inches.
Device Management: This refers to the ability to manage external hardware seamlessly, including printers/encoders, sensors, and other external hardware that can be operated and maintained through web-based operator environments.
Platform Integration: Modern RFID tech can be applied to a wide array of platforms including desktop, web-based systems and mobile systems quickly and easily. RFID inventory tracking software systems can be integrated to work with different kinds of ERP, WMS, and different proprietary systems like Oracle, MySQL, MS SQL Server, XML, FTP/SFTP, and Web Services.
Customization: Modern RFID systems are customizable, meaning that operators have control over their inventory management systems to ensure they meet the unique needs of their business. They also offer scalable solutions that range from enterprise-wide applications to select area monitoring.
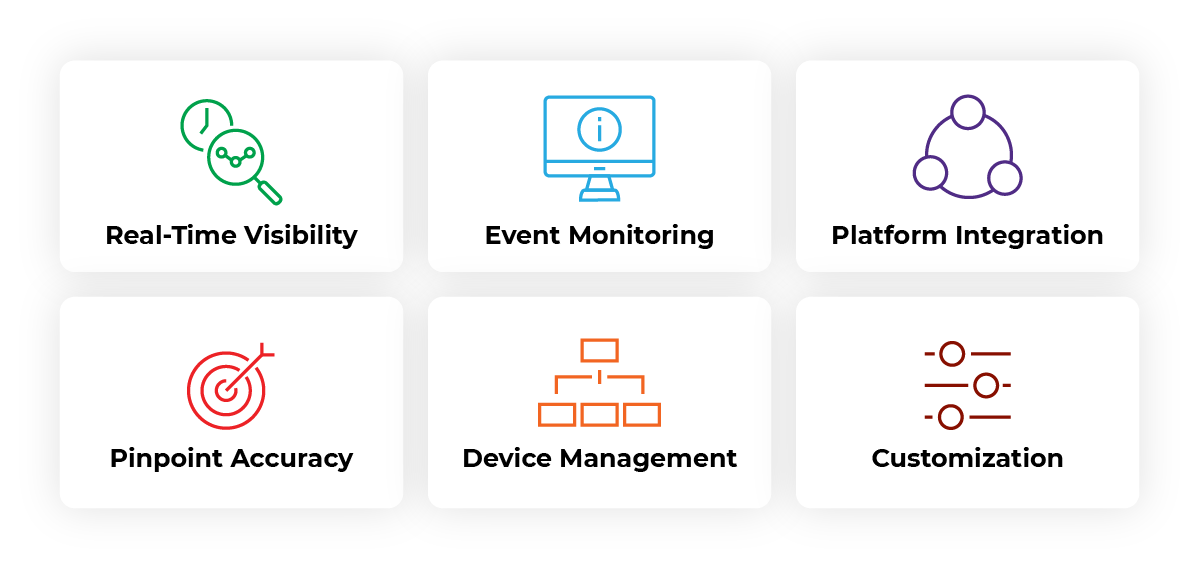
How To Set Up an RFID Inventory Management Solution
When coupled with Electronic Product Code (EPC), RFID technology is a major element of the most efficient method of tracking products from the manufacturing facility to the showroom floor, and beyond. The following is a general outline of how to set up the RFID inventory management system for retailers.
- Gather RFID System Components – Before the RFID inventory system can be implemented, retailers must purchase the necessary tools and materials. The basic required elements are RFID readers, an RFID printer, RFID tags, and an RFID inventory management software like PortalTrack Software to track the RFID tags.
- Place the RFID Tags – Once the retailer has acquired all the necessary components, it is time to set up the RFID inventory system. The first step is to physically place the RFID tags on the existing tags of each and every product. This step is most important as there is no way to track merchandise if it has not been marked with an RFID tag. One crucial decision is the placement, particularly on boxes of merchandise. It is important that these tags can be quickly and easily scanned. It is also important that these tags don’t cover up any other crucial information, such as printed barcode labels. In many instances, the RFID tag will be inside the barcode label, but that’s not always the case. When thinking about tag placement, also consider how it will appear to the customer, whether the tag can be adjusted after the initial placement, and how well it will work throughout the sales process as you apply it.
- Install RFID Readers – There are 2 types of RFID readers, fixed and mobile. Fixed readers and antennas may be used at specified checkpoints to gather data while mobile readers are traditionally used for inventory and search functions.
- Set Up Asset Tracking Software – Next, retailers must install and implement the software necessary to track the products marked with the RFID tags. MSM Solutions’ PortalTrack software is vendor-neutral and ties together the RFID system components from the programming of the EPC RFID tags through the printing and placement, to reading the RFID tags. With the use of an interface, these RFID tags can be monitored and tracked, providing immediate reading and reporting on the amount of inventory present in the store.
Pros and Cons of RFID
Benefits of RFID Inventory Management
- Enhanced Tracking and Visibility: Traditional inventory methods often rely on manual counts or barcode scanning, which can be time-consuming and prone to errors. RFID systems automatically track products as they move through the supply chain, offering real-time insights into inventory levels. This means businesses can quickly locate specific items, reduce misplaced stock, and improve overall accuracy.
- Efficient Inventory Counts: With RFID, physical inventory counts become much faster and more efficient. Instead of manually counting items or scanning individual barcodes, employees can use RFID readers to quickly scan entire shelves or rooms, capturing data on all products within range in a matter of seconds.
- Reduced Human Error: Since RFID doesn’t rely on manual processes, the chances of errors due to miscounts, mislabeled products, or data entry mistakes are greatly reduced. This means more accurate inventory levels and fewer discrepancies.
- Theft and Loss Prevention: RFID tags can be employed as security measures. If an item that hasn’t been checked out or purchased comes near an exit or designated point, the system can trigger an alarm, reducing the chances of theft.
- Optimized Stock Levels: With more accurate data on inventory, businesses can ensure they have the right amount of stock on hand. This reduces carrying costs associated with overstocking and minimizes stock-outs, which could lead to lost sales.
- Streamlined Receiving and Shipping: When shipments arrive or leave a warehouse, RFID allows for quick and automatic verification of contents, ensuring that the right products are received or sent out.
As we step into the future of retail, RFID inventory management systems have made it possible for a variety of large-scale retailers to easily track all aspects of their inventory. For example McKinsey & Co. created the “retail store of the future” to further explore the many ways in which RFID technology can be useful within the retail sector. The store is called Modern Retail Collective and the goal of the store is to evaluate newer technologies such as fit predictor software, smart mirrors, and the acceptance of future payment methods such as cryptocurrencies. This venture was made possible by companies such as MSM Solutions, a company that has been intricately involved in the creation and development of RFID technology for many years. The following is a guide on how to set up these RFID inventory management solutions for small and medium retailers.
Challenges of RFID Inventory Management
- Initial Investment
RFID systems require upfront costs for tags, readers, and software, but many businesses find that the long-term savings in labor and accuracy make it a worthwhile investment and ROI can be achieved in one year. - System Integration
Some businesses may need to update their inventory management software to fully integrate RFID tracking, but most modern WMS and ERP systems now offer built-in RFID integration compatibility. - RF Signal Considerations
RFID performs well in most environments, but certain materials like metal and liquids can require specialized tags or reader adjustments for optimal accuracy.
Despite these potential challenges, the cost of doing nothing can often be greater than the investment in RFID technology. Inefficient tracking, manual errors, and stock discrepancies can lead to lost revenue, increased labor costs, and supply chain disruptions. Fortunately, advancements in RFID technology, software compatibility, and tag design continue to make implementation more accessible. Businesses considering RFID inventory management should assess their operational needs, existing systems, and long-term ROI before making the transition.
RFID vs. Barcodes: What Is the Difference?
RFID and barcode technology play essential roles in inventory management, and the best choice depends on your specific operational needs. While RFID enables automated, real-time tracking, barcodes remain a cost-effective and widely used solution for various industries.
When to Use RFID
✔ High-Volume Inventory Tracking – RFID is ideal for warehouses, distribution centers, and retail stores that need to track large quantities of inventory accurately and fast.
✔ Real-Time Visibility – Companies that require instant updates on stock levels benefit from RFID’s ability to scan multiple items at once without manual input.
✔ Asset Tracking & Security – RFID helps monitor returnable assets, tools, and high-value inventory while improving loss prevention.
✔ Hands-Free Automation – RFID works well in environments where automation is key, such as smart warehouses and automated retail checkouts.
When to Use Barcodes
✔ Lower-Cost Inventory Management – Barcodes are a cost-effective solution for businesses that need a reliable tracking method without the higher upfront investment of RFID.
✔ Smaller Operations & Retail – For businesses with smaller inventories or that require item-by-item scanning, barcodes provide a simple and effective method.
✔ Compatibility & Industry Standard – Many existing POS systems, inventory software, and supply chain processes already use barcode scanning, making it easy to integrate.
✔ Short-Term or Temporary Tracking Needs – For one-time events, pop-up retail, or short-term inventory projects, barcodes offer an efficient, flexible solution.
Integrating RFID & Barcode Technology
Many businesses use both RFID and barcodes together to optimize inventory tracking. For example:
- Retailers may use RFID for back-end stock management and barcodes for customer checkout.
- Warehouses can track bulk shipments with RFID but use barcodes for individual item tracking.
Both technologies offer valuable inventory management capabilities, and the right choice depends on your business needs, budget, and operational requirements.
RFID vs. Barcodes
Factor | RFID | Barcode |
---|---|---|
Best For | High-volume inventory tracking | Smaller operations and retail stores |
Scanning Method | Reads multiple tags at once without line-of-sight | Requires manual, one-by-one scanning |
Real-Time Visibility | Provides instant inventory updates | Stock levels update only when scanned |
Automation and Hands-Free Use | Works in automated warehouses and checkout systems | Requires manual scanning by employees |
Security and Loss Prevention | Detects stolen or misplaced items automatically | No built-in loss prevention features |
Integration and Compatibility | May require RFID-compatible WMS/ERP software | Easily integrates with most POS and inventory systems |
Cost Considerations | Higher initial investment, but long-term efficiency savings | Lower upfront costs, but requires more manual labor |
Best Use Cases | Warehouses, distribution centers, retail stockrooms, asset tracking | Retail checkout, short-term tracking, small-scale inventory |
RFID Inventory Management Case Studies: Real-World Applications and Success Stories
Businesses across manufacturing, retail, healthcare, logistics, and automotive are leveraging RFID technology to streamline operations, improve inventory accuracy, and enhance supply chain visibility.
Conclusion
Overall, the RFID inventory management system is, by far, the most efficient method of tracking inventory for retailers of all kinds. Although retailers may be a bit reluctant to totally revamp their existing inventory systems, doing so would immediately and drastically reduce the time spent searching for inventory, reduce theft and shrinkage, and help retailers gain a better perspective on their customers and to which types of products to order in the future. Either way, companies such as MSM Solutions are a vital component of making the worries and burdens of inventory management a thing of the past. Rather than continuing with the dated methods of tracking inventory, RFID technology allows retailers to set up a system that easily manages all aspects of inventory without the need for extensive training and at minimal cost. No matter how large or small one’s inventory may be, installing an RFID inventory system can make it possible for retailers to immediately put an end to inventory confusion.
Contact MSM Solutions, your RFID inventory management tracking experts today.
RFID Inventory Management FAQs
How does RFID work in supply chain management?
RFID improves supply chain operations by offering real-time insights into inventory movement at every stage. RFID tags, attached to products or pallets, are scanned automatically by RFID readers, updating stock levels without manual input. This helps businesses track shipments, prevent stockouts, reduce human error, and improve operational efficiency. Many companies use RFID to optimize warehouse management, shipping verification, and retail inventory replenishment.
For businesses looking to improve supply chain accuracy, MSM Solutions can help assess whether RFID is the right fit for your operations.
How Much Does an RFID Inventory Management System Cost?
RFID implementation costs depend on several factors, including hardware, software, installation, and ongoing maintenance. Here’s a general breakdown of what businesses can expect:
Hardware Costs
Passive RFID tags: Typically range from $0.04–$1.00 per tag, depending on quantity and material.
Active RFID tags: Cost between $15–$50+ per tag, especially for specialized tracking needs.
RFID readers: Prices vary based on type—handheld readers generally cost $1,500–$3,000, while fixed scanners range from $2,500–$5,000.
Additional equipment: RFID-enabled printers, antennas, and network infrastructure may add to overall expenses.
Software Costs
Businesses need RFID inventory management software to process and analyze data such as MSM Portal Track.
Costs can range from basic tracking solutions from hundreds of dollars to enterprise-level integrations that scale into six figures, depending on custom features and complexity.
Installation & Maintenance
Setup costs depend on system complexity—passive RFID installations are generally simpler, while active RFID requires more calibration and infrastructure.
Ongoing maintenance is typically minimal for passive systems, though active RFID setups may require battery replacements and periodic servicing.
Getting a Customized Cost Estimate
Since every business has unique needs, RFID pricing varies based on scale, industry, and integration requirements. MSM Solutions offers customized RFID implementation strategies to ensure businesses get the right solution for their budget and operational goals.
Contact our RFID experts today.
How accurate is RFID inventory?
RFID inventory management systems can achieve accuracy rates of 98-99%, significantly reducing errors caused by manual counting or barcode misreads. Unlike traditional methods, RFID allows for bulk scanning, real-time updates, and hands-free tracking, improving stock visibility across warehouses, retail stores, and distribution centers.
For companies looking to improve inventory accuracy, MSM Solutions offers tailored RFID solutions to enhance tracking efficiency.